Porosity in Welding: Identifying Common Issues and Implementing Ideal Practices for Prevention
Porosity in welding is a prevalent issue that usually goes unnoticed till it causes considerable problems with the stability of welds. This usual defect can jeopardize the toughness and sturdiness of bonded structures, positioning safety and security risks and causing pricey rework. By understanding the origin creates of porosity and implementing efficient avoidance approaches, welders can considerably enhance the top quality and reliability of their welds. In this discussion, we will check out the vital factors contributing to porosity development, analyze its destructive effects on weld performance, and go over the very best techniques that can be adopted to minimize porosity incident in welding processes.
Usual Root Causes Of Porosity
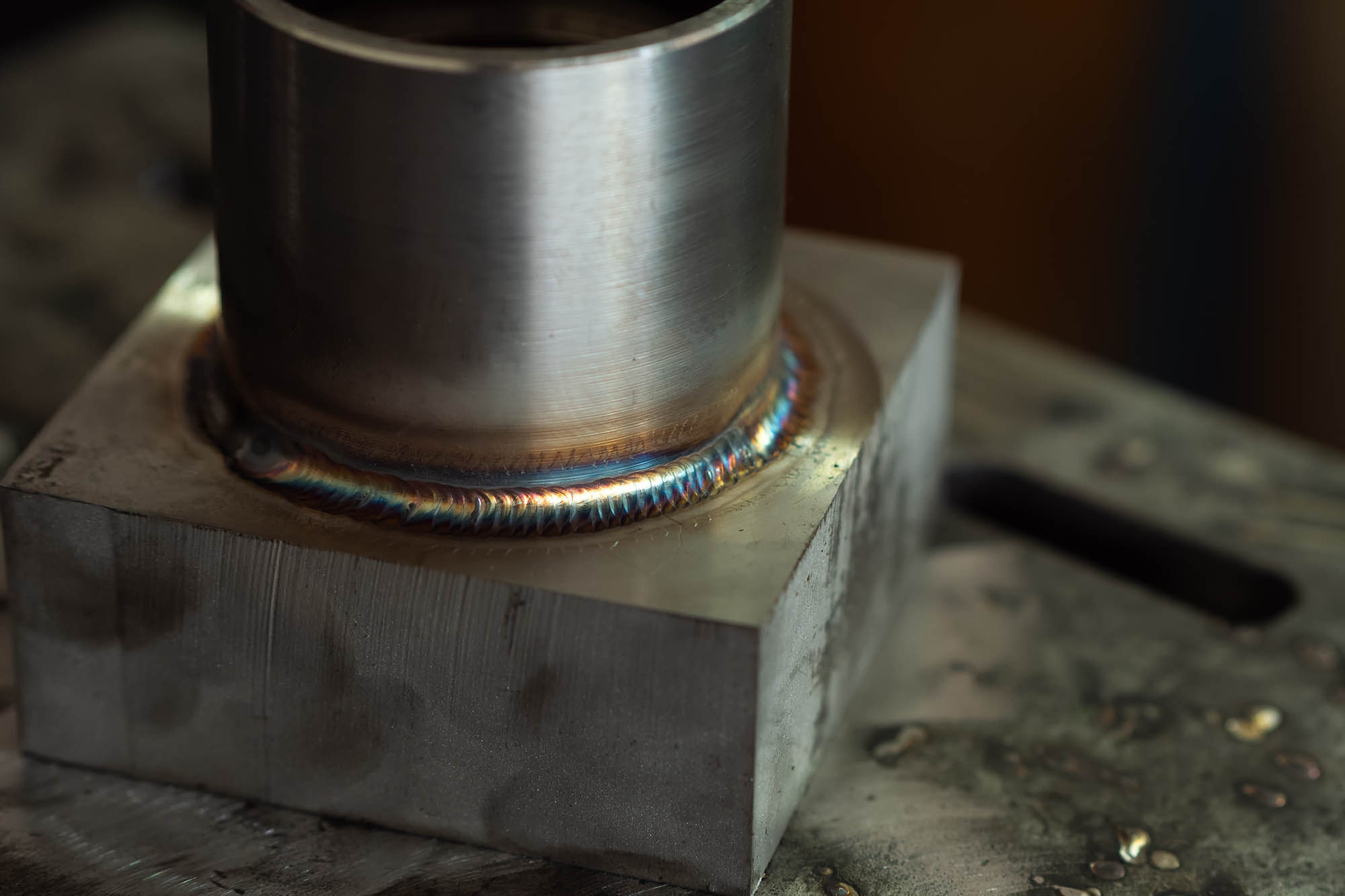
An additional frequent perpetrator behind porosity is the presence of pollutants externally of the base metal, such as oil, grease, or corrosion. When these contaminants are not efficiently gotten rid of before welding, they can vaporize and end up being entraped in the weld, causing flaws. Making use of unclean or wet filler materials can introduce pollutants right into the weld, contributing to porosity issues. To reduce these typical reasons for porosity, comprehensive cleaning of base steels, appropriate securing gas option, and adherence to ideal welding parameters are vital methods in attaining high-quality, porosity-free welds.
Impact of Porosity on Weld Quality

The presence of porosity in welding can dramatically endanger the structural honesty and mechanical residential properties of welded joints. Porosity develops voids within the weld steel, weakening its general strength and load-bearing capability.
Among the main effects of porosity is a decrease in the weld's ductility and sturdiness. Welds with high porosity levels tend to exhibit lower influence stamina and lowered ability to warp plastically prior to fracturing. This can be particularly concerning in applications where the bonded parts go through vibrant or cyclic loading problems. Porosity can hamper the weld's capacity to properly transmit forces, leading to premature weld failure and prospective safety risks in essential frameworks. What is Porosity.
Best Practices for Porosity Prevention
To enhance the architectural honesty and top quality of bonded joints, what particular steps can be executed to reduce the occurrence of porosity throughout the welding procedure? Porosity prevention in welding is essential to ensure the honesty and toughness of the final weld. One their explanation effective technique is correct cleaning of the base metal, getting rid of any type of contaminants such as rust, oil, paint, or dampness that might lead to gas entrapment. Ensuring that the welding tools is in good problem, with clean consumables and ideal gas circulation rates, can additionally considerably reduce porosity. In addition, preserving a secure arc and managing the welding parameters, such as voltage, present, and travel speed, aids create a regular weld pool that decreases the risk of gas entrapment. Making use of the appropriate welding strategy for the particular product being welded, such as readjusting the welding angle and gun setting, can further stop porosity. Regular assessment of welds and immediate remediation of any kind of issues determined throughout the welding process are necessary practices to stop porosity and generate top quality welds.
Significance of Appropriate Welding Methods
Carrying out proper welding strategies is critical in ensuring the structural honesty and quality of bonded joints, constructing upon the foundation of effective porosity avoidance measures. Too much heat can lead to increased porosity due to the entrapment of gases in the weld pool. In addition, utilizing the proper welding parameters, such as voltage, present, and take a trip speed, is critical for achieving audio welds with marginal porosity.
Additionally, the selection of welding process, whether it be MIG, TIG, or stick welding, ought to straighten with the particular needs of the task to guarantee optimum outcomes. Proper cleaning and prep work of the base steel, as well as selecting the ideal filler product, are likewise crucial components of efficient welding strategies. By adhering to these best practices, welders can lessen the danger of porosity development and generate premium, structurally audio welds.
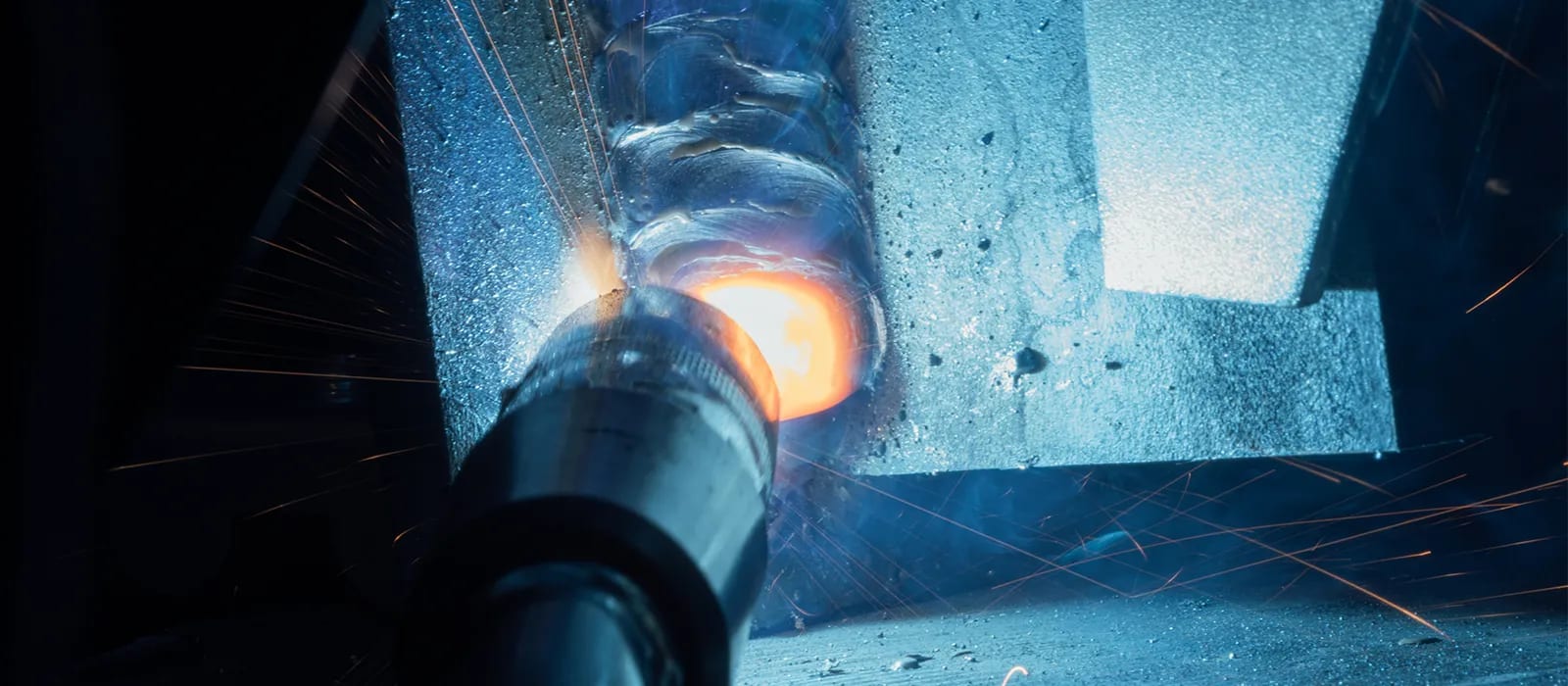
Testing and High Quality Control Steps
Quality control procedures play a critical duty in validating the honesty and integrity of bonded joints. Checking treatments are vital to find and stop porosity in welding, making sure the stamina and toughness of the end product. Non-destructive testing approaches such as ultrasonic screening, radiographic testing, and aesthetic inspection are frequently employed to recognize possible flaws like porosity. These methods permit the analysis of weld high quality without jeopardizing the integrity of the joint. What is Porosity.
Post-weld examinations, on the various other hand, assess the final weld for any defects, consisting of porosity, and validate that it fulfills defined requirements. Carrying out view website a detailed over at this website high quality control plan that includes thorough screening procedures and inspections is paramount to reducing porosity concerns and making sure the general high quality of welded joints.
Verdict
To conclude, porosity in welding can be a typical issue that influences the top quality of welds. By determining the typical sources of porosity and implementing ideal methods for prevention, such as correct welding methods and screening procedures, welders can guarantee high quality and trusted welds. It is necessary to prioritize avoidance methods to minimize the event of porosity and preserve the honesty of welded frameworks.
Comments on “How to Identify What is Porosity in Welding and Improve Your Technique”